How Can You Effectively Remove Moisture From Compressed Air?
In the world of industrial applications and pneumatic systems, the quality of compressed air is paramount. Moisture in compressed air can lead to a myriad of problems, from equipment corrosion to product contamination, ultimately affecting operational efficiency and safety. Whether you’re running a small workshop or managing a large manufacturing facility, understanding how to effectively remove moisture from compressed air is crucial for maintaining the integrity of your systems. In this article, we will explore various methods and technologies designed to tackle this common challenge, ensuring that your compressed air remains clean, dry, and reliable.
Overview
Compressed air systems are often susceptible to moisture accumulation due to the natural condensation that occurs when air is compressed. This moisture can wreak havoc on machinery, leading to increased maintenance costs and potential downtime. To combat this issue, it’s essential to implement effective moisture removal strategies that can enhance the performance and longevity of your equipment.
From simple filtration techniques to advanced drying technologies, there are numerous approaches available to keep your compressed air dry. Understanding the principles behind these methods not only helps in selecting the right solution for your needs but also empowers you to optimize your compressed air system for peak performance. As we delve deeper into the various options, you’ll discover the best practices for moisture removal that can safeguard your operations and improve overall efficiency.
Understanding the Sources of Moisture in Compressed Air
Moisture in compressed air can originate from several sources, including atmospheric humidity, condensation in air receivers, and the process of air compression itself. Understanding these sources is crucial for effectively addressing moisture issues.
- Atmospheric humidity: Compressed air systems draw in air from the environment, which inherently contains moisture. The warmer the air, the more moisture it can hold.
- Condensation: As air is compressed, it heats up and can hold more moisture. However, upon expansion or cooling, this moisture can condense into water droplets, leading to contamination.
- Heat of compression: The process of compressing air generates heat, which can affect moisture levels. If not managed, this moisture can eventually cause system failures or damage.
Methods for Removing Moisture from Compressed Air
There are several effective techniques for removing moisture from compressed air systems. Each method has its advantages and should be selected based on the specific requirements of the application.
- Air Dryers: These are the most common solutions for moisture removal. They can be categorized into:
- Refrigerated Dryers: These cool the compressed air, causing moisture to condense and be removed.
- Desiccant Dryers: These use a desiccant material to absorb moisture from the air. They are suitable for applications requiring very low dew points.
- Filters: Installing coalescing filters can help capture water droplets and particulates before they reach the end-use equipment.
- Drain Traps: Automatic drain traps can be installed at various points in the compressed air system to remove accumulated moisture.
- Heat Exchangers: By cooling the compressed air, heat exchangers can facilitate moisture condensation, which can then be drained away.
Method | Pros | Cons |
---|---|---|
Refrigerated Dryer | Effective for moderate moisture levels; relatively low maintenance. | Less effective in extremely low temperatures; may require additional pre-filtration. |
Desiccant Dryer | Excellent for very low dew points; versatile for various applications. | Higher operational costs; requires periodic replacement of desiccant material. |
Coalescing Filter | Removes particulates along with moisture; easy to install. | Requires regular maintenance and replacement. |
Drain Traps | Automates moisture removal; reduces manual labor. | Initial installation cost; potential for mechanical failure. |
Monitoring and Maintenance
Regular monitoring and maintenance of compressed air systems are essential for preventing moisture-related issues. Implementing a routine inspection schedule can help ensure that moisture removal equipment is functioning correctly.
- Dew Point Monitoring: Keeping track of the dew point can help in assessing the effectiveness of moisture removal systems.
- Regular Maintenance: Ensure that filters, dryers, and drain traps are routinely serviced and replaced as needed.
- System Audits: Conducting periodic audits of the entire compressed air system can identify potential moisture sources and areas for improvement.
By employing these methods and maintaining a proactive approach, businesses can effectively manage moisture in compressed air systems, ensuring optimal performance and longevity of equipment.
Understanding the Importance of Moisture Removal
Moisture in compressed air systems can lead to various issues, including corrosion, reduced efficiency, and equipment damage. It is crucial to manage moisture levels to ensure the longevity of tools and machinery.
Methods for Removing Moisture from Compressed Air
Several techniques can effectively reduce moisture in compressed air systems. These methods can be used independently or in combination for optimal results.
Cooling and Condensation
This method utilizes the principle that air cools when it expands, allowing moisture to condense and separate from the air stream.
- Refrigerated Air Dryers:
- Operate by cooling the compressed air to a temperature below its dew point.
- Moisture condenses and is removed through a drain.
- Aftercoolers:
- Installed immediately after the air compressor.
- Cool the compressed air before it enters the dryer system.
Desiccant Drying
Desiccant dryers employ materials that absorb moisture from the compressed air.
- Types of Desiccants:
- Silica Gel: Commonly used for low humidity applications.
- Activated Alumina: Effective in a wider range of humidity levels.
- Operation:
- Compressed air flows through a vessel containing desiccant material.
- The desiccant adsorbs moisture, and the air exits dry.
Membrane Dryers
Membrane dryers utilize selective permeation to remove moisture.
- Functionality:
- Compressed air passes through a membrane that allows water vapor to permeate while retaining dry air.
- Suitable for applications requiring low moisture levels.
Prevention Techniques
Implementing preventive measures can significantly reduce moisture accumulation in compressed air systems.
- Proper System Design:
- Design systems with proper drainage and avoid low points where moisture can accumulate.
- Regular Maintenance:
- Schedule regular inspection and maintenance of dryers and filters.
- Condensate Management:
- Install automatic drain valves on filters and dryers to ensure moisture is removed continuously.
Choosing the Right Equipment
Selecting the appropriate moisture removal equipment depends on several factors:
Criteria | Considerations |
---|---|
Volume of Compressed Air | Determine the flow rate requirements. |
Operating Environment | Assess humidity levels and temperature. |
Cost | Balance between initial investment and long-term savings. |
Maintenance Needs | Evaluate the ease of upkeep for selected equipment. |
Monitoring and Control
Continuous monitoring of moisture levels is essential for effective management.
- Dew Point Monitors:
- Install sensors to measure dew point and ensure air quality.
- Regular Testing:
- Perform periodic checks on moisture content in compressed air.
By employing these strategies, organizations can effectively manage moisture in compressed air systems, ensuring reliable operation and extending equipment lifespan.
Expert Strategies for Moisture Removal in Compressed Air Systems
Dr. Emily Chen (Mechanical Engineer, Air Quality Solutions Inc.). “To effectively remove moisture from compressed air, implementing a multi-stage filtration system is essential. This system should include a pre-filter to capture larger particles, followed by a refrigerated dryer that cools the air to condense water vapor, and finally a desiccant dryer to absorb any remaining moisture.”
Mark Thompson (Industrial Equipment Specialist, Compressed Air Technologies). “Regular maintenance of your compressed air system is crucial. This includes checking and replacing filters, ensuring proper drainage from moisture traps, and monitoring the performance of dryers. A well-maintained system significantly reduces moisture buildup.”
Linda Martinez (Process Engineer, Precision Manufacturing Group). “Utilizing heatless desiccant dryers can be a game changer for moisture control. These dryers operate without the need for external heat, making them energy-efficient while effectively removing moisture from the compressed air, ensuring optimal performance in sensitive applications.”
Frequently Asked Questions (FAQs)
How can I effectively remove moisture from compressed air?
To effectively remove moisture from compressed air, utilize a combination of air dryers, filters, and separators. Refrigerated dryers cool the air, causing moisture to condense, while desiccant dryers absorb remaining humidity. Inline filters can capture any residual water droplets.
What types of air dryers are available for moisture removal?
The primary types of air dryers include refrigerated dryers, desiccant dryers, and membrane dryers. Refrigerated dryers are suitable for general applications, desiccant dryers excel in low-temperature environments, and membrane dryers are ideal for specific applications requiring minimal moisture.
How often should I maintain my air drying system?
Regular maintenance of your air drying system is crucial. It is recommended to inspect and service the system every three to six months, depending on usage. This includes checking filters, replacing desiccants, and ensuring the proper functioning of the dryer.
What are the signs that my compressed air has excess moisture?
Signs of excess moisture in compressed air include water droplets in the air lines, corrosion on equipment, reduced efficiency in pneumatic tools, and inconsistent performance of air-operated devices. Regular monitoring can help identify these issues early.
Can moisture in compressed air affect my equipment?
Yes, moisture in compressed air can significantly affect equipment performance. It can lead to corrosion, rust, and damage to pneumatic tools, as well as reduced efficiency and increased downtime due to maintenance and repairs.
Is it necessary to use a moisture separator in my compressed air system?
Using a moisture separator is highly recommended in compressed air systems. It helps to remove bulk water from the air stream before it reaches the dryer, enhancing the overall efficiency of the drying process and protecting downstream equipment from moisture-related damage.
Removing moisture from compressed air is essential for maintaining the efficiency and longevity of pneumatic systems and tools. Moisture can lead to corrosion, reduced performance, and potential damage to equipment. To effectively eliminate moisture, several methods can be employed, including the use of air dryers, filters, and proper system design. Each method has its own advantages and is suitable for different applications, depending on the level of moisture control required.
One of the most effective solutions for moisture removal is the installation of refrigerated air dryers, which cool the compressed air to condense and remove water vapor. Desiccant dryers are another option, utilizing moisture-absorbing materials to achieve extremely low dew points. Additionally, incorporating filters and separators can help capture any remaining water droplets before the air reaches the end-use application. Regular maintenance of these systems is crucial to ensure optimal performance and moisture control.
It is important to consider the specific needs of your application when selecting a moisture removal method. Factors such as the required air quality, the volume of air being compressed, and environmental conditions should all influence your choice. By implementing the right strategies and equipment, businesses can significantly reduce moisture levels in compressed air systems, leading to improved efficiency and reduced operational costs.
Author Profile
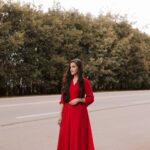
-
I’m Lora Gross, and I’m delighted to share this journey with you. My vision has always been simple: to create a warm, inclusive space where women can explore ideas, learn about wellness, and discover tips that truly resonate.
Here, you’ll find thoughtful insights that honor the multifaceted nature of womanhood. Whether you’re looking for guidance on maintaining your well-being, discovering new beauty techniques, or simply celebrating the power of femininity, our content is crafted with you in mind.
Our foundation remains rooted in the belief that every woman deserves to feel confident, cared for, and celebrated. We draw upon our history of community, style, and empowerment while expanding our horizons to cover the diverse interests and needs of today’s women. This isn’t just about trends it’s about sharing real stories, practical advice, and heartfelt connections that make a difference.
Latest entries
- April 10, 2025General LifestyleCan You Still Claim Maternity Leave After Being Fired?
- April 10, 2025General LifestyleWhat Do Women Wear in Turkey? A Guide to Traditional and Modern Fashion Choices
- April 10, 2025General LifestyleHow Should You Properly Wear a Maternity Belt for Comfort and Support?
- April 10, 2025Skincare & Acne CareDo Pre Workouts Really Cause Acne? Unpacking the Connection!